Tái chế pin giúp giảm một nửa lượng khí nhà kính so với khai thác mỏ
Một nghiên cứu mới của Đại học Stanford cho thấy quy trình tái chế pin lithium-ion theo mô hình
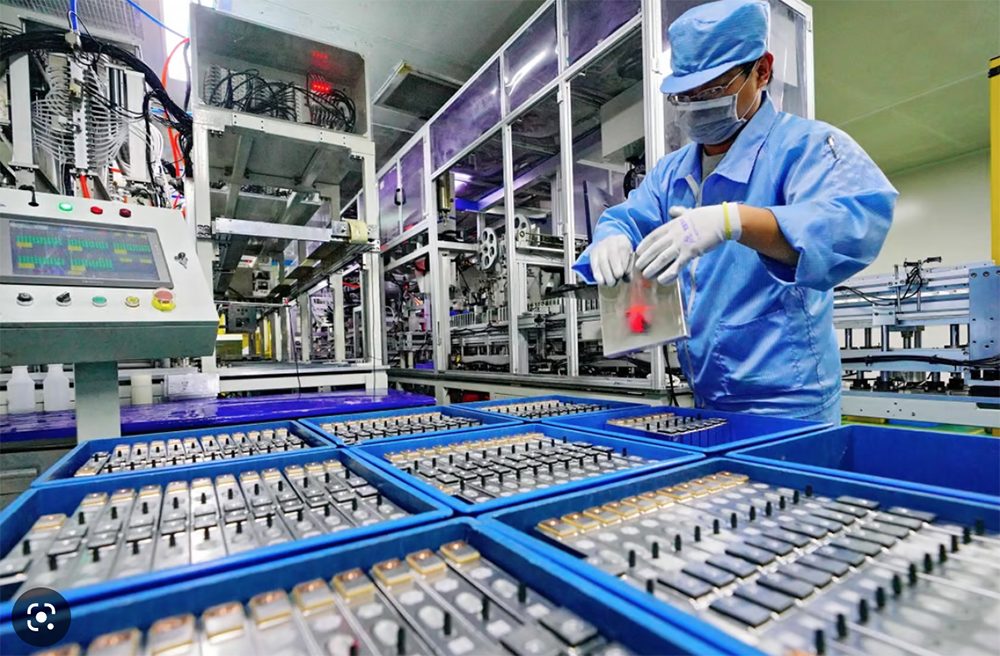
Một nghiên cứu mới của Đại học Stanford cho thấy quy trình tái chế pin lithium-ion theo mô hình tuần hoàn giúp giảm đến 50% lượng khí nhà kính (GHG) so với phương pháp khai thác kim loại truyền thống. Đây là kết quả so sánh giữa hai chuỗi cung ứng: một bên là khai thác và tinh chế kim loại từ quặng tự nhiên, và một bên là thu hồi vật liệu từ pin đã qua sử dụng.
Nghiên cứu được công bố cuối tháng 1 bởi nhóm tác giả tại phòng thí nghiệm Tarpeh của Stanford. Trong bối cảnh ngành xe điện và năng lượng tái tạo đang phát triển nhanh chóng, sản lượng pin lithium-ion toàn cầu được dự báo đạt 2,4 TWh vào năm 2030, với khoảng 82% nhu cầu đến từ xe điện. Tuy nhiên, tốc độ tăng trưởng này cũng làm gia tăng nguy cơ thiếu hụt các vật liệu then chốt như lithium, coban và niken, đồng thời đặt ra thách thức lớn về xử lý pin sau sử dụng.
Theo nhóm nghiên cứu, việc thu hồi kim loại từ pin cũ không chỉ giúp giảm áp lực khai thác mỏ mà còn mang lại hiệu quả môi trường rõ rệt. Trong quá trình tái chế, lượng nước và năng lượng tiêu thụ chỉ bằng khoảng 25% so với quy trình khai thác và tinh chế truyền thống.
Dữ liệu về tái chế được nhóm nghiên cứu lấy từ Redwood Materials – công ty tái chế pin lithium-ion lớn nhất Bắc Mỹ, đặt tại Nevada, Mỹ. Redwood sử dụng các nguồn năng lượng tái tạo như thủy điện, địa nhiệt và điện mặt trời trong quy trình sản xuất. Trong khi đó, dữ liệu khai thác mỏ được điều chỉnh theo mô hình GREET năm 2021 – công cụ tiêu chuẩn do Phòng thí nghiệm Quốc gia Argonne phát triển để đánh giá khí thải và mức tiêu thụ năng lượng của các chuỗi cung ứng.
Ngoài việc nghiên cứu pin thu gom từ thiết bị điện tử và phương tiện giao thông, nhóm tác giả cũng phân tích vật liệu thải loại trong quá trình sản xuất pin. Kết quả cho thấy nếu tái chế ngay từ khâu sản xuất, lượng phát thải GHG giảm đến 81%, đồng thời tiết kiệm được 88–89% nước và năng lượng.
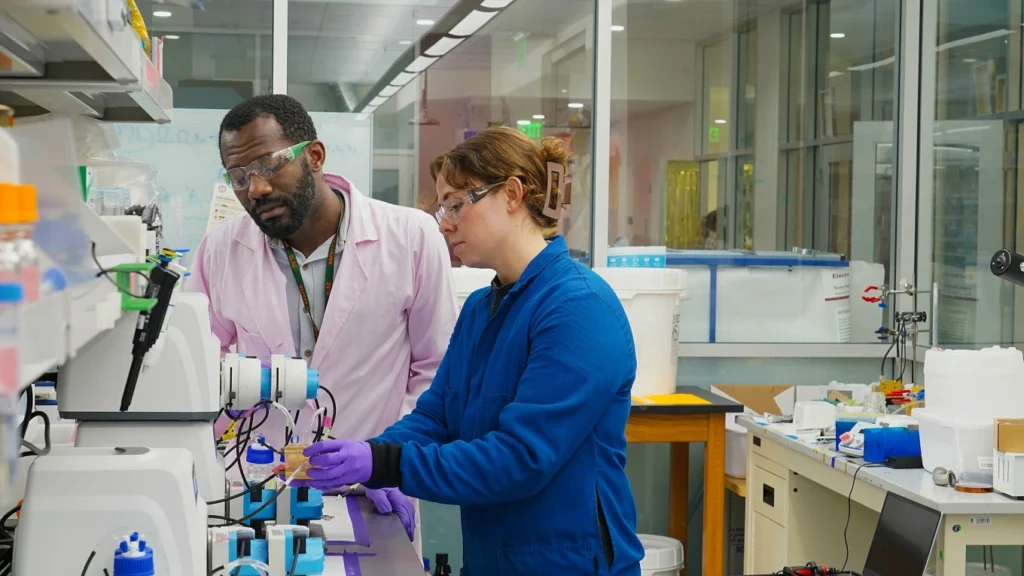
Khoảng cách vận chuyển nguyên liệu cũng là yếu tố đáng kể. Hiện tại, 80% nguồn cung coban toàn cầu đến từ Cộng hòa Dân chủ Congo, sau đó được chuyển sang Trung Quốc để tinh chế. Lithium chủ yếu được khai thác tại Australia và Chile, rồi cũng được vận chuyển đến Trung Quốc. Trung bình, quãng đường vận chuyển kim loại trong chuỗi cung ứng pin hiện nay vào khoảng 57.000 km – tương đương 1,5 lần vòng quanh Trái Đất.
Ngược lại, việc tái chế pin đã qua sử dụng tại một cơ sở tinh chế nội địa, ví dụ như ở California, chỉ cần vận chuyển khoảng 225 km. “Sự khác biệt này cho thấy tiềm năng cắt giảm đáng kể lượng phát thải từ logistics nếu các cơ sở tái chế được phân bố hợp lý”, Tiến sĩ Michael Machala – đồng tác giả nghiên cứu và nhà khoa học tại Viện Nghiên cứu Toyota, nhận định.
Phó giáo sư William Tarpeh – tác giả chính – cho rằng, để chuẩn bị cho khối lượng pin khổng lồ cần xử lý trong tương lai, điều quan trọng là phải thiết kế ngay từ bây giờ một hệ thống thu gom và tái chế toàn diện, hoạt động với mức tác động môi trường thấp nhất. Điều này bao gồm cả việc cân nhắc khả năng tái chế ngay từ khâu thiết kế pin – một hướng tiếp cận đang ngày càng được các nhà sản xuất pin và xe điện quốc tế quan tâm.
Hiện tại, Mỹ đã tái chế thành công 99% pin axit chì, trong khi tỷ lệ này với pin lithium-ion mới chỉ ở mức 50%. Tuy nhiên, pin lithium-ion chứa các vật liệu có giá trị kinh tế cao hơn nhiều, gấp khoảng 10 lần so với pin axit chì, tạo ra tiềm năng thương mại lớn nếu được khai thác đúng cách.
Nguồn: TechXplore (Stanford University), Nature Energy
Tác giả chính: William Tarpeh
Thời điểm công bố: Tháng 1/2024